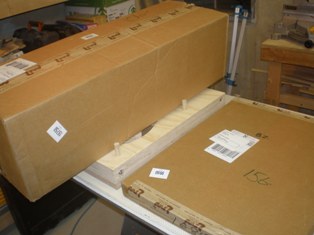
12/08/09 - The kit finally arrives. In these two boxes, weighing less than 15 lbs., is a guitar. |
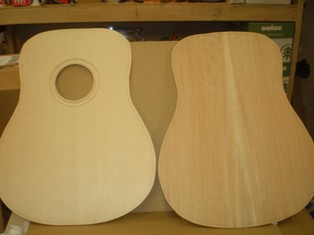
12/08/09 - The flat box was the top and back, nicely packed with
cardboard and peanuts to keep them safe. Since I need to wait a couple
weeks so they acclimate to my temp & humidity, I "stickered" them
to keep them as flat as possible. You can see on the top that the
soundhole rosette has been pre-routed. |
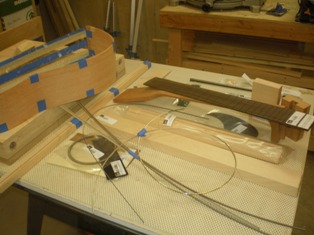
12/08/09 - The other box held the rest of the kit. The loop on top is
the fretwire. The long thin pieces are the edge binding and purfling
(thin decorative edge banding). The neck has the fretboard sitting on
top of it, and the neck and tail block just beyond it. The long plastic
bag in the middle holds the braces. The prebent sides are on the left,
they were taped to help them keep their shape. |
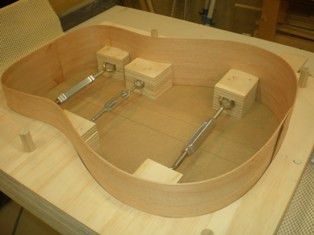
12/08/09 - Step 1! Since I need to wait a couple weeks, I needed to put
the sides in the mold so they would hold their shape. I made the mold
out of three layers of plywood, then added the blocks and turnbuckles
to keep the sides spread. The sides are left long. The next step will
be to trim them to length. |
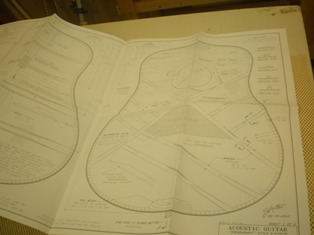
12/08/09 - The plans. These and an acrylic template which matches will guide me through the build process. |
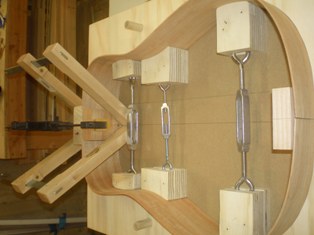
12/18/09 - I have now trimmed the sides to length. Here I am dry-fitting the neck and tail blocks.
|
12/18/09 - Here is how the neck mounts to the neck block. |
12/18/09 - Dry-fitting. I still need to cut the neck block length down a bit prior to gluing it in. |
12/19/09 - Gluing in the neck and tail blocks. |
12/19/09 - Once the blocks are glued in, I planed the ends of the sides
down to the height of the blocks. This is to get the sides to the width
of the guitar minus the top & back. |
12/20/09 - I'm not sure why I took this picture, other than it shows
the top side of the sides. All the others show the back side. On the
left you can see the mortise in the neck block. |
12/20/09 - Here I am starting to radius the sides. An acoustic guitar
is not flat. The top and back are actually domed, to give them
strength. So here I am sanding the sides to that radius. |
12/20/09 - This is a 30' radius dish with sandpaper stuck to it. You
can see as I sand only the ends are touching so that is where the
sawdust is. |
12/20/09 - Here you can see where the light is shining under the
middle. I need to carefully plane and then sand the edges so that they
meet this 30' radius all around. |
12/20/09 - There it is. No more light! |
12/20/09 - Another technique for seeing where the sanding is needed. I
chalk the whole edge, then lightly sand, and where the chalk is left
isn't touching the dish yet. |
12/20/09 - Once the top and back are radiused (the top gets a 15'
radius, much less pronounced than the back), the next step is to glue
on kerfing. This thin strip of wood has kerfs cut in it so it will
conform to the curves of the sides. The purpose is to give a wider edge
for gluing the top and back on later. |
12/20/09 - About 100 clothespins with rubber bands added to them are the clamps needed. |
12/20/09 - The kerfing is left a little higher than the sides, they
will then be sanded like before to put the radius edge on them. |
12/20/09 - Here I am setting up to start working on the guitar back.
The back is laying on the 15' radius dish, which is in what is called a
go-bar deck. On top of the back is a reinforcement strip that will be
glued in. |
12/20/09 - Here is how the go-bar deck works. Fiberglass rods called
go-bars are used to clamp the brace in place, forcing the back into
that radius. The go-bar deck is two pieces of plywood, the top is
adjustable to allow for different heights of the braces. |
12/20/09 - Here you can see the difference between flat and a 15'
radius. I'm getting a little ahead of myself here, but needed to do
something while the glue was drying on the kerfing. Before I glue the
reinforcement strip and bracing on the back I need to rout and glue in
a decorative strip to the outside of the back. Stay tuned..... |
12/21/09 - Setting up to rout for the decorative backstrip. If building
from scratch, this strip can sometimes be glued in between the two
halves. In my case, I have to do it afterwards. |
12/21/09 - The strip is about the same thickness of the back, so I want
to rout about 2/3 through. After the strip is glued in, I will scrape
and sand it flush. |
12/21/09 - Here is the strip glued in. The strip is wood, and the pattern goes all the way through. |
12/24/09 - Now I have to get the strip flush with the back. I chose to
scrape it down with a scraper. It took quite a bit since the scraper
shaves an extremely small amount with each pass. |
12/24/09 - With the kerfings all glued in it was back to the sanding
dishes. Had I known how much work this would be I wouldn't have left
them quite so high. It took about 20 minutes of twisting the whole form
back and forth to get the kerfing sanded flush with the side. |
12/24/09 - Here is a good picture where you can kind of see the angle of the edge. |
12/24/09 - Then it was time to work on the back transverse braces.Here
they are layed out where they will go. I had to mark their locations
90° to the center line on the inside of the back. |
12/24/09 - The bottoms of the braces come flat, I have to radius them
to the 15' curve. First I marked the curve with a pencil, then planed
the ends close to the line to get them close. |
12/24/09 - Then I rubbed them back and forth on the radius dish to sand
the 15' radius into the bottom. Here you can see the #2 brace prior to
planing and sanding, and the #1 brace behind it is done. |
12/24/09 - Here is the go-bar deck in actual use. The #1 brace hasn't
been glued at this point because I don't have enough bars. This forces
the back into the 15' radius. |
12/28/09 - Here I am gluing in the center brace on the back. I am using
thin strips of plywood because the brace is soft and I don't want the
go-bars to leave dents. |
12/28/09 - Next up are these "popsicle stick" braces. Some builders
actually use popsicle sticks, I chose to cut my own thin strips from
extra spruce I had. These help to stiffen the body and to help prevent
the sides from splitting. |
12/28/09 - Before I can work on the braces for the top, I have to fit
and glue the rosette. My kit came pre-routed, but I could have easily
done this. The top is sitting on a piece of plywood. |
12/28/09 - Here the rosette is cut to length and dry-fitted. The seam
ended up closer than this looks, and will be covered by the fretboard
anyway. |
12/28/09 - Here the rosette purfling is glued in. |
12/28/09 - After gluing in the rosette I placed it in the go-bar deck
to hold it down. The rosette ended up inset a little in places, I will
have to scrape and then sand everything flush. The top is still a
little thick still anyway. |
1/3/10 - After scraping and sanding, the rosette and purflings are flush with the surface of the top.
|
1/3/10 - Closeup. |
1/3/10 - Beginning to layout the inside of the top for the braces.Here the X-braces have been notched in a half-lap joint. |
1/3/10 - Closeup of the joint. Each brace has been notched halfway. This is the key brace to keep the top from collapsing. |
1/3/10 - The rest of the braces layed out. |
1/3/10 - Here I have trimmed the braces to length and roughed the
scallops on the ends. The X-braces and the transverse shoulder brace
(just above the sound hole) will be notched into the kerfing on the
sides of the guitar. The others are cut shorter to fit just inside of
the kerfing. |
1/3/10 - I rough cut the scallops on the scroll saw, and here I am
refining them with the spindle sander. The traditional way to do this
is to carve/chisel them after they are glued to the top. I don't have
the curved chisel to do that, and at $60 I decided to take a different
approach. I will refine them with a regular chisel later. |
1/3/10 - Gluing in the X-brace. These and the shoulder brace are
radiused as shown earlier. The smaller braces will be glued in flat. |
1/10/10 - Came down to find water had been leaking from the furnace
humidifier for 24 hours. Click on the picture to see where I note the
water line. About 1/2" covered this area. I had accidentally pulled the
drain tube off when I checked it the day before. |
1/10/10 - Unfortunately, the mold with the guitar sides was on the
floor, resting against a workbench. I had the thought to pick it up the
other day so I wouldn't step on it or something. I wish I had! The
water wicked up through the seam and got to the guitar sides.
Fortunately, this was the only damage. Everything else that got wet
isn't important. |
1/10/10 - Here is the water mark on the sides. The larger picture is
marked. This was taken about an hour or so after I pulled it out of the
mold, and it was already dry to the touch. |
1/10/10 - After 2 hours of water cleanup, finally some actual guitar
work. Here I am shaving the ends of the braces down to final thickness.
|
1/17/10 - The top is now finished. The bottom tone bar is now carved.
and I put a hole in the shoulder brace above the sound hole to allow
for an allen wrench to get to the truss rod in the neck after assembly.
I should have drilled that hole prior to gluing the brace on, it would
have been easier. All that is left is to clean up the pencil marks and
sign the inside of the top. |
1/17/10 - The brace ends are sanded to the final thickness. I made the
block on the right with a groove down the center. That groove is .10"
(3/32). The tape protects the back. When the tape touches the back it
smudges the pencil lines and I know to stop. |
1/17/10 - Now the block is used to set the depth of the router bit.I am
using an additional piece of plywood with a slot in it to give me more
surface for the router to ride on. |
1/17/10 - Now I use the router to cut the notches in the kerfing where
the brace ends will meet it. Without the plywood I would be trying to
balance the router on an edge that is just 3/8" wide. |
1/17/10 - I also used this high speed rotary tool with a tiny bit to get in the corners... |
1/17/10 - ...and here is why. I chose to only rout the kerfing and not
the guitar side too. I then cut the brace end so that it meets the
side. Most builders just cut the notch all the way through. |
1/17/10 - And now the back fits and is ready to be glued on. |
1/17/10 - Here is what the brace looks like in the notch. |
1/17/10 - A little wider view. |
2/28/10 - I finally made it back down to the shop. Here I am
pre-forming the purfling that will later be glued around the edges of
the top. These are made of wood, and I wanted to get them formed to the
shape. It will make it easier to install later. |
2/28/10 - They were starting to twist and curl a little. This is just insurance that they will make these bends later. |
2/28/10 - Getting ready to glue the back on. The tape is to protect the sides if excess glue drips on them. |
2/28/10 - I cut the darker ring out of masonite so the rods wouldn't leave marks in the back. (or break it!) |
2/28/10 - All glued up. I ordered more bars awhile ago so I would have enough for this step. |
2/28/10 - Several hours later and the back is glued on successfully.
Here you can see how well the braces fit in the notches. I have a
little excess glue to clean up, but I am happy with this progress. |
3/10/10 - Time to glue the top on. I did forget to do something before I did this, but I can work around that mistake. |
3/10/10 - After a few hours for the glue to dry, it is finally time to
remove the spreaders. I made sure they were small enough to fit through
the soundhole before I glued the top on. It wasn't easy reaching my arm
to the furthest one, but they came out ok. |
3/10/10 - Before removing the body from the mold, I needed to trim off the excess on the top and bottom. |
3/10/10 - Here you can see the progress. |
3/10/10 - A milestone! The body is out of the mold. Next up for it will be purfling and binding. |
3/10/10 - The label I made for the inside. I also signed the inside of the top, which is traditional for luthiers to do. |
3/10/10 - Also today I cut out my logo. This is pearl shell (it comes
from the inside of shells). It is only partially shiny because there is
residue on it from the paper I had glued on it. I will be inlaying this
in the headstock. I probably should have made this a little thicker, it
would have made routing the inlay easier. |
3/10/10 - Another shot of the water damage from January. I hope this sands out, if not I will have to stain the back and sides. |
|
|